Screw chuck
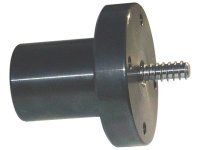
You can make servicable screw chucks yourself out of wood on your lathe! These are handy for holding such projects as wooden fruit, toy wheels or anything which can be held by a small central hole.
The Masterchuck has dual purpose jaws which have dovetails shaped on both the inside and the outside gripping areas. This allows either contracting grip or expanding grip, using the same jaws. The wood must be the correct diameter to fit the curvature of the jaws and shaped with the correct angle of "dovetail".