 |
Categories |
 |
|
 |
Quick Find |
 |
|
 |
Manufacturers |
 |
|
|
|
Free information and data sheets |
 |
|
 |
Choose from the following and it will appear below.
Setting up your first woodturning workshop
Lathe features in more detail
Quality and Weight of Machine In woodturning, vibration is the enemy. A good lathe will be massive
and rigid to damp down the vibration. Light sheet metal construction is to be
avoided and cast iron is the best. Good bearings and smooth running are the
hallmarks of a high class machine. Buy the best you can afford not the biggest.
There is great pleasure and satisfaction to be had from using a quality tool
or a quality lathe. Pleasure in use is what you are looking for yes?
Lathe capacity
Biggest is not always the best. A large heavyweight lathe can be clumsy to use
and many professional turners have a small lathe in addition to a full size
machine for small to medium jobs. Most projects will fit nicely on a lathe with
around 36" (900mm) between centres and 10" to 12" diameter swing
over the bed, so for your first lathe I suggest you should be looking at this
size of machine. You should get best value in this size range too because lathes
of this capacity are made in large quantities for a competitive market. Go bigger
if you have a specific requirement but do not sacrifice weight, rigidity and
quality of engineering to get bigger capacity.
Length between centres
Some manufacturers offer a number of options on the bed length, for example
20", 30" and 40" length between centres. A very long bed is not
necessarily desirable as the machine will take up more space and a long lanky
bed may flex and vibrate. 36" is about right for general work. Remember
that long turnings such as standard lamps and four poster bedposts are generally
made up in shorter sections and joined.
For the odd occasion when something very long has to be made, the tailstock
can be positioned on an improvised wood block beyond the end of the lathe bed.
You could reserve bench space for this purpose.
Swing over the bed
If the machine has a pivoting head allowing large diameter faceplate work then
10" diameter swing (5" centre height) over the bed will cope well
with most furniture spindle turning and chuck work so could be considered adequate.
However if you want to turn large hollow "vessels" in a chuck then
you will need more space over the bed. Many experienced turners start with the
blank held between centres. If the blank is irregularly shaped like a burr (burl
to some people!) then it an advantage to experiment with different orientations
at first to get the best shape. If you want to try this then you will need at
least 12" diameter space over the bed. Remember that the toolrest banjo
can reduce the space available but it is often possible to manage with it placed
to one side out of the way.
Bowl turning capacity
Bowl turning capacity is often limited by the weight and rigidity of the machine
and by the minimum speed available (a 15" bowl should not go much faster
than 450 rpm) rather than by the paper specification. Large bowl blanks are
always out of balance and anything over about 15" diameter needs a very
low speed to be safe when roughing down the blank to shape. For hobby use I
would say that 15" diameter by 5" deep bowl capacity is generous.
Pivoting headstocks and sliding headstocks
A pivot headstock is fast becoming standard on all but the biggest modern lathes.
It is more comfortable hollowing bowls (and many other projects) with the head
turned towards you because you do not have to lean over the lathe bed. Pivoting
the head also prevents the lathe bed getting in the way of the handle of the
bowl gouge. I like to use a gouge ground square across at the end and this style
of grind requires the handle of the tool to be well down when hollowing.
Make sure the swivel mechanism is solid and locks securely so that rigidity
is not sacrificed. It should be easy to return the headstock to the "straight
ahead" position so that the centres line up accurately. An indent pin to
reposition the headstock is a useful feature.
Some headstocks can both pivot and also slide along to the middle of the bed.
If the head is in the middle of the bed and pivoted to face towards you then
the toolrest banjo is removed and positioned to the left of the headstock for
turning the outside of the bowl. For large bowls you need to use a bowl turning
extension arm to gain access to the centre of the bowl.
Another advantage of a sliding head is that the lathe can be positioned into
a left hand corner of the workshop to save space. If you slide the headstock
and bowl along the bed to the right, there will be space for you to stand while
you turn the outside of the bowl. Remember you have to work on the left of the
bowl because the bowl is turning anti clockwise.
Bowl turning attachments
These support the toolrest for bowl turning when the head is pivoted round.
They should be rigid enough not to twist in use. Ideally they should slide back
out of the way or pivot out of the way when they are not being used. They are
often sold as an optional "extra". But why buy a pivot head lathe
without a bowl attachment? They should be standard equipment. Most of them are
designed to be used with the headstock turned round through 90° although
I have seen 180° ones. Floor standing bowl rests have to be very heavy to
be successful and are not popular.
Non pivot headstocks with double ended spindle
If a lathe has a double ended spindle, big bowls can be turned "outboard"
on the left of the headstock. This allows the turner full freedom of movement
and there is no limit to the diameter because there is no bed in the way. This
arrangement is often seen on older lathes on the secondhand market.
The disadvantage is that you will need to spend more on accessories because
the threads are different at each end. For example, a chuck which fits the inboard
end will need an adaptor to enable it to fit on the outboard end.
Rotation (looking into the bowl) is clockwise when on the outboard end as opposed
to anticlockwise on the inboard end so you will have to get used to turning
the wrong way! It might be easier if you are left handed. The other objection
with outboard turning (only with cheap lathes) is that the bearing at the outboard
end of the spindle is generally smaller and weaker than the inboard bearing
when it should really be stronger to cope with heavy out-of-balance loads.
Speed range
Look for a good range of speeds and convenient speed change. Four or five speeds
are enough. You need a low speed for initial turning of large, heavy bowl blanks
which are, more often than not, out of balance. A low speed is also required
for wine table tops, bread boards etc. Around 400 rpm or less is required. About
2000 rpm is adequate at the high end unless you want to do a lot of lace bobbins.
Higher speeds will only wear away your tool edges faster.
Lathe spindle and threads
Look for . .
(a) A standard thread size to allow you to fit a wide range of accessories from
a choice of suppliers e.g. 1" x 8 threads to the inch.
(b) A "register" which is a plain unthreaded section between thread
and shoulder. Its purpose is to ensure accuracy and true running of chucks
and faceplates. Some spindles are threaded all the way up to the shoulder and
are not so accurate.
(c) A Morse Taper socket for small accessories. Lathes without a morse taper
socket in the spindle nose are generally to be avoided as it is difficult to
buy and fit accessories such as drive centres. A No. 2 or 3 morse taper in the
spindle nose is more desirable than a No. 1 morse. A No.1 morse socket is rather
small and drill chucks and drives can easily spin under load.
(d) An easy means for removing taper mounted fittings such as a through hole
for knocking them out or an ejector collar as on Record lathes. A through hole
is better because you can use a "drawbar" to retain fittings in the
taper socket.
(e) Easy spindle locking to allow unscrewing of faceplates etc. If the locking
device also offers indexing then that is a bonus.
Bearings
Look for . . .
(a) Pre-loaded Taper-roller or angular-contact ball bearings.
(b) A bearing at both ends of the spindle. Many imported lathes have bearings
at only one end, sacrificing rigidity.
Most medium price lathes have two deep groove ball races but taper roller bearings
or angular contact races with pre-loading are more desirable. Pre-loading means
that the front bearings and rear bearings are tightened against each other to
take out any fore and aft free play. A very small but undesirable amount of
free-play is inherent in ordinary ball races. Pre-loading has to be just right
so as to remove free play but not strain the bearings too much. It generally
takes the form of a threaded collar at the rear of the spindle which you can
adjust.
Plain or "solid" bearings take the form of a bronze or white-metal
bush in which the spindle runs. There are no balls or rollers so friction can
cause heat and take power from the motor. They need regular and efficient lubrication
and can also demand frequent adjustment. On some lathes there are no oil seals.
Over enthusiastic application of oil can result in surplus oil spraying on the
work (and on you). They however have one big advantage over ball bearings -
they are very good at damping down vibration. In fact a correctly designed plain
bearing made to the highest engineering standards is the finest bearing you
can get. The most expensive woodturning and engineering lathes can have plain
bearings.
My advice is to avoid plain bearings unless they have oil seals and automatic
oiling and and go for ball races on medium price lathes.
It is best, for rigidity, to have a long spindle with the bearings widely spaced.
The worst arrangement is a double bearing at only one end of the spindle such
as found on some popular imported lathes. Although these lathes boast an outboard
(left hand end) spindle for bowl turning there is no support at all for the
left hand end of the spindle! Unfortunately it is now quite hard to find a budget
lathe with a bearing at the left of the pulleys to support the end of the spindle.
The modern tendency with Far Eastern lathes is to provide a pair of ball races
spaced apart around 4" but placed at the right of the pulleys. This is
for convenience and cheapness of manufacture and assembly. It is OK for most
projects but you will have vibration problems on bowls and hollow forms.
Desirable extras for the ideal headstock
These are an indexing facility, easily changed belt, quick locking of spindle
for unscrewing faceplates and chucks, reversing facility (see below) and a hole
right through the spindle for knocking out taper shank drive centres. I like
to have the push button switch located on the headstock so I can always reach
it even if the head is pivoted round. A handwheel is very useful because I often
like to be able to turn the spindle by hand when the lathe is stopped - to inspect
the polished finish on my work for example.
Variable speed headstocks
These are now common and many turners favour them for the convenience of quick
speed change without the need for messing about with pulleys and belt guards.
There are two basic types - electronic and mechanical. The mechanical type is
usually of the sort that uses special vee pulleys which can open and close.
The vee belt is made to rise higher up in the vee gap between the pulley faces
to simulate the effect of a larger pulley and conversely to sink lower down
into the gap to get the effect of a smaller pulley. Two pulleys are used - the
drive pulley and the driven pulley. One pulley closes as the other opens and
by this means the ratio of the drive is altered to give infinitely variable
speed. The drive has to be well designed and engineered to give good reliable
results. Cheap drives can suffer from problems.
Electronic variable speed drives now use a 3 phase motor driven by a box of
complicated electronics called an "inverter" which is capable of producing
a three phase supply of variable frequency and voltage from your standard single
phase mains supply. It so happens that the speed of an induction motor is governed
by the frequency of the A.C. supply which powers it. The electronics are used
to vary the frequency and thus the speed. These drives can reduce the speed
to extremely low revs - very handy for initial shaping of out-of-balance pieces,
or thread chasing. Electronic drives are controlled by their own internal microcomputer
and are programmed to provide sophisticated facilities such as soft start, braking,
and overload protection.
They can provide just as much torque at the lowest speed as they can at high
speed and this is proclaimed as a virtue. In fact they are not as good as the
mechanical drives in this respect as a good mechanical drive provides proportionately
more torque as the speed is reduced, in the same way as a mechanical gearbox
or a multistep pulley system. Bowl turners need lots of torque at low speeds
and they should be warned that some electronically driven lathes are inadequate
for this purpose. One way to get good torque at low speed with an electronic
drive is to use a big motor. If you are a serious bowl turner you will need
3/4 horsepower minimum at 500 r.p.m. which implies 3 H.P. at 1500 r.p.m. (horsepower
is torque multiplied by speed) Anything less and you will not be able to take
a heavy roughing cut with a bowl gouge.
A cheaper way to get around this problem is to have both an electronic speed
control and a multi step pulley system to maintain reasonable torque at low
speeds by going to a lower ratio. With this dual arrangement a 1 horsepower
motor and inverter will be ample for most woodturners especially if the inverter
is of the modern type which can give a torque boost at low revs.
By contrast, a much cheaper mechanical variable speed drive with only a 1/2
horsepower motor can give a surprisingly good account of itself even when bowl
turning.
Motor and electrics
The best motor to have is T.E.F.C which means totally enclosed fan cooled. This
is desirable to guard against dust. It should be an induction motor and the
4 pole type (about 1450 rpm) is preferable to 2 pole (about 2850 r.p.m.). It
should not mind being stopped and started frequently. Assuming you are on standard
household single phase mains the motor should have a large starting capacitor
and centrifugal switch for high starting torque. The cheaper type of motor with
a small start and run capacitor and no centrifugal switch is not as good.
You should look for at least 1/2 horsepower, preferably more for large bowl
turning. Anything bigger than around 2 horsepower will need special wiring but
most lathes will just plug into a 13 amp wall socket.
The starter switch should be push button for convenience with a protruding STOP
button which is always within easy reach. The switch should have overload protection
and no-volt release. No volt release or NVR means that if you have a temporary
power cut, the lathe will not start unexpectedly when the power comes on. The
switch must be sealed against fine sawdust which has a habit of finding its
way between the contacts.
For safety the switch should be within easy reach even when the head is pivoted
around when you are working at the extreme end of the machine. It is best if
the switch is attached to the headstock of a pivoting head lathe. It is worth
considering fitting a kickbar along the lathe base to cut out the motor in an
emergency.
Reversing the lathe motor
It is handy to be able to reverse the spindle for finishing work. Scraping and
sanding, especially on bowls, tends to lay the fibres of the wood down in one
direction and it is difficult to obtain a good finish. Reversing the lathe and
sanding off the fibres the other way does the trick.
Not many lathes have this facility because of the danger of the faceplate or
chuck unscrewing. The Myford Mystro lathe has a locking device on the spindle
which prevents unscrewing so that bowls can be reversed at will or even turned
to shape in reverse if required.
Tailstocks
The tailstock is important. Avoid a one with an awkward "thumbwheel"
control or one with too little travel for drilling holes. Reject a tailstock
without a Morse taper socket. A design of tailstock which is definitely to be
avoided is one which has a threaded barrel which actually rotates when you tighten
it up. This is because you cannot fit a drillchuck for drilling holes - essential
for many projects such as peppermills.
The tailstock should have :
(a) Cast iron body.
(b) A hole right through, at least 5/16" diameter, to allow deep drilling
with the lamp auger.
(c) A barrel which is prevented from rotating in its housing by a keyway. Some
cheap imported lathes have a primitive one piece threaded barrel which could
spin out of control if you attempted to mount a drill chuck on the end and drill
a hole!
(d) A Morse taper socket, preferably No 2 but No 1 is just acceptable, for mounting
centres and drill chucks. Drill chucks do not hold well in a No 1 morse socket.
(e) A barrel with a long travel to help with drilling and a proper handwheel
which is easy to turn.
(f) Accurate location in the bed so as to line up true with the headstock spindle
and centre.
(g) secure locking of the barrel and secure clamping to the bed
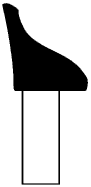 |
Toolrest and bracket (or banjo)
Should be strong and rigid. The banjo should slide easily on the bed and
lock securely. Cam locking to the lathe bed is excellent and is worth looking
for.
All locking levers should be convenient to use and be out of the way of
the workpiece and the turning tools. Ratchet handles are popular and can
be altered so as to be out of the way when tight.
Toolrests come in all sorts of shapes and sizes.
I like the section shown
because I can rub my finger along the front edge of the rest to guide the
tool in a straight line. This comes in useful for turning straight cylinders
and flat discs for platters, table tops, cheese boards etc. The top edge
should be nicely rounded and allow the tool handle to come down to about
45 degrees from the horizontal without fouling the clamping lever.
You should be able to move the toolrest close to the centre line of the
bed for turning small objects. The toolrest should raise or lower half an
inch above or below the centre height.
The toolrest stem should be at least ¾" diameter, preferably
1", so the toolrest does not spin round in use. The toolrest top should
be level. |
Lathe bed
The bed should be straight and true. The headstock drive centre and tailstock
centre should line up accurately or you will find it difficult to drill holes.
The headstock spindle and tailstock barrel should be parallel to the bed.
The best lathe beds are solid cast iron. It is the best material, not only because
of its weight and rigidity but also because . . .
(a) it exhibits low friction.
(b) It always comes machined - hopefully straight and true.
(c) The above two factors mean that the tailstock and toolrest slide beautifully
when moved. This adds greatly to the ease of use of the lathe and can only be
appreciated if you have been turning for some while. Also the machined surfaces
give the tailstock centre a better chance of lining up perfectly with the spindle
drive centre.
(d) The wearing surfaces are generally larger, particularly where the tailstock
slides along the bed. This will give the lathe a longer and more accurate life.
(e) It is easy to fit home made accessories such as steady rests to the flat
surface of a cast bed.
(f) Cast iron does not seem to rust so easily which is an advantage if the lathe
is kept in a damp shed.
Lathe beds are often made from steel or steel tube for economy. This is OK but
you will discover that the tailstock and banjo will not slide so easily as on
a cast iron bed and the clamping arrangements are not so easy to use.
Provided that the same weight of metal is used, steel tube is as strong or better
than solid. Square section is preferable to round. This is because square section
gives a greater wear resistance and it is easier to fit home made accessories,
jigs and fixtures such as steadies.
You should have a feel of the lathe bed before you buy a lathe to make sure
that it does not flex appreciably in the middle. It is not a matter of strength
but one of resistance to vibration.
Beds longer than about 36" are likely to vibrate somewhat so it is better
not to buy a long bed lathe unless you have a real need for it. You might have
to jam a wedge of wood underneath the middle of the bed if you have a problem
with it.
Some budget lathes have two fairly light steel tubes to serve as the bed. You
can upgrade such a lathe very cheaply by purchasing a length of solid steel
bar at your local steel stockist. Steel comes in 10 foot lengths so you should
take a hacksaw with you and cut it in half when you buy to get it into your
car (it's greasy so take some newspaper). You will end up with a heavier and
longer lathe bed with a smoother surface than the original for just a few pounds.
Next page
|
|
 |
|
|
 |
0 items |
 |
|
|
 |
Information |
 |
|
 |
Info Sheets |
 |
|
 |
Bestsellers |
 |
|
|